As mentioned just over a week ago, this season sees sees John Lewis unveil its fourth yet first full scale exclusive collection designed by the great Joe Casely-Hayford. Recognised for his innovation and ability to produce definitive future classics, Casely-Hayford's range celebrates the best of British sartorialism through a series of unique collaborations with some of the UK's leading heritage companies. For AWll, Casely-Hayford continues to build on the strong foundations laid in the three previous capsule collections. Having established a strong following through exclusive collaborations with some of the UK’s finest heritage manufacturers. From key seasonal outerwear created out of fabric woven in England by the Abraham Moon Mills in Yorkshire to a great Fair Isle pattern Yoke pullover that is knitted in 100% Wool by crafts people in the Donegal Mountains and shirting showcasing one of the first ever Liberty prints to be digitally created, the collaboration celebrates all that these islands have to offer. Through this series of collaborations with specialists and true craftsman, the range showcases unique cloths whilst reintroducing a few updated British classics to the wider audience of the high street. During my excited ramblings I mentioned the fact that I was invited to watch the Moons craftsmen at work at their Guiseley factory. I eagerly followed and snapped away at each well honed and practiced process from start to finish.
Before I offer an abundance of 'factory porn' and talk you through the processes of what makes Moon fabric so special I have to acquaint you with the brand and give you a little background. The name might not feel that familiar on first reading but I'm quite sure that you've seen or indeed worn their work without even knowing it. In addition to apparel, its textiles are used for growing accessories and furnishings arms. Abraham Moon and Sons is a family owned company that assures luxurious quality whilst continuously evolving to meet the ever changing needs of the industry. The current Managing Director is John Walsh, the fourth generation of the family which succeeded the Moon dynasty. Since 1837 when Abraham Moon founded the company, bales of raw wool have been arriving at their factory to begin the process of creating beautiful fabrics. Located in Yorkshire, traditional home of the English cloth mills, the company is unique in being a fully vertical mill, with dyeing, blending, carding, spinning, weaving and finishing processes all taking place on one site. State of the art manufacturing allied to a highly skilled workforce enable a wide diversity of fabrics to be manufactured at competitive price levels – a prerequisite to success in today’s market place. The craftsmanship and well honed skills are essential to the product and it was a pleasure to be able to watch it all unfold in a space that has seen the same processes come together for over two centuries. It is little wonder why Casely-Hayford partnered with them.
As a self confessed factory pervert, you can only imagine how many photographs I took as I was guided through the nooks and crannies of this well oiled assembly line of craftsmanship. I have managed to hone them down and will now use them to guide you through the main processes to turn fleece in to stunning fabric.
----------
From fleece to fabric
The first stage begins with the delivery of the finest raw wool which is from sought across the globe and delivered to their site in Guiseley. The merino lambswool is predominantly from South Africa and the Shetland quality pure new wool is from New Zealand. The raw wool then goes to the dye house, to be dyed using precise combinations and a secret cocktail of dye, pressure, temperature and time. They can currently dye their wool in over five hundred different shades and colours. Within the Dye House they keep a library of shade standards and recipes to ensure continuity of each glorious colour year and year.
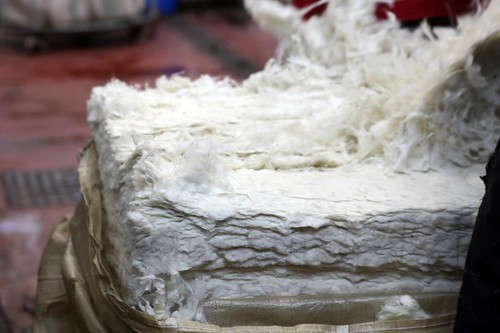
I was infatuated with the texture of the fleece as I watched the men unpack it before on embarking on the dyeing process.
Part of me wanted to throw myself in to the dyeing cauldrons.
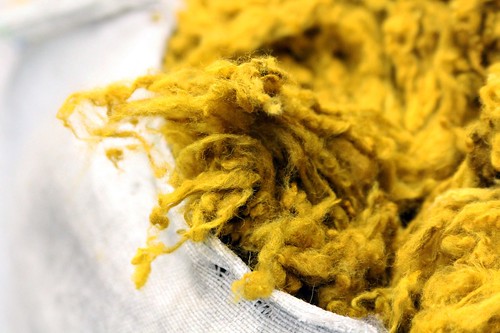
Just one of the hues that caught my eye,
Now, the real secret to creating beautifully rich colour is in the blend. During this stage up to seven different coloured wools can be used in the recipe for each yarn. It is this process that gives tweeds, heathers and plaids their wonderfully unique and rich texture. Moons prides itself on its arsenal of hues and I was dazzled by the spectrum on offer...
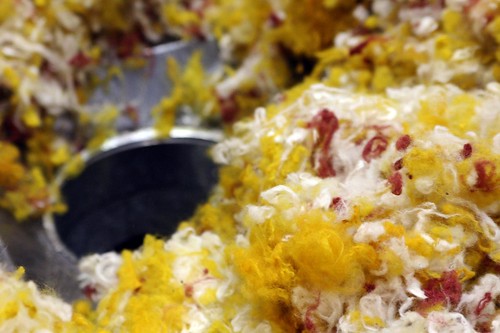
Once blended, the mix is then transferred to the carding area.
The next process, carding is essential in producing soft, smooth fabrics. The blended wool lubricated with a little water and oil is run through a series of combed rollers that tease the fibres one way and then the other. Whilst providing alignment and conformity, the process also rids the wool of any last impurities and ensures the finished fabrics are smooth and soft to the touch.
A close up of the blended wool before it is passed through the carding rollers...
The carding machine
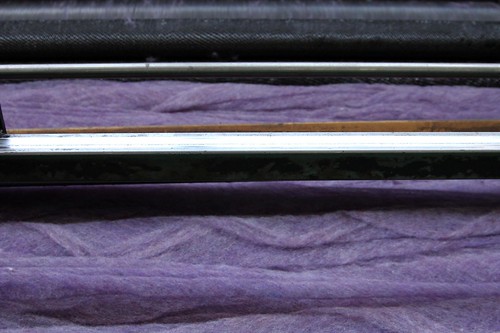
A sea of rollers teasing the fibres each and every way.
The rich web of coloured wool is then spun in to a huge range of dazzling yarns. Their six frames draw out the wool and put a precise number of twists per inch in to the wool, resulting in a fine but ultimately strong thread ideal for fabrics used in clothing and furnishings alike. The yarn is then wound on to cones going through a check to ensure continuity. Any faults are cut out of the thread and the ends are thermally joined together to produce a yarn that will weave in to smooth fabrics. The cones, holding up to sixteen thousand metres of yarn are then ready to be sent to warping and weaving.
The wool begins to take on a more familiar appearance.
The cones of yarn are then wound over a swift and a warp is made for weaving. This can be a complicated process depending upon the intricacy of the pattern in the finished fabric. I was treated to a to a variety during my time in the mill. Precise lengths of different coloured yarn can be required in a single vertical thread and up to two thousand threads may be required for a width of fabric. Mind blowing. These have to all be held in exact order to ensure accurate and uniform patterns and designs. The warping process is one of the most beautiful...
Warped fabric ready to be weaved.
The weaving process is the loudest and is where the real magic happens. The space is filled with a percussion of machinery. The work here might be less hands on than it once would’ve been but it is no less impressive and bewildering to the eye. It is here where many different yarns are woven together in intricate weaves to create stunning fabrics. The mill uses Rapier looms, to take the weft (horizontal thread) across the warp threads and they are capable of weaving up to thirty thousand metres of cloth per week. The machines work at a dizzying pace and volume but the below shots document the process in a much more peaceful light...
An array of fabrics were being weaved during my time in the mill.
Now, we are almost there. Newly woven fabric is then scoured, milled and dried. The oils that were used to aid manufacture of the fabric are removed. This is when the wonderful and luxurious feel of these fabrics begins to become apparent. The final step sees each length of fabric finished by careful pressing, using steam and specialised equipment to remove any shrinkage and complete the process of creating remarkable fabrics.
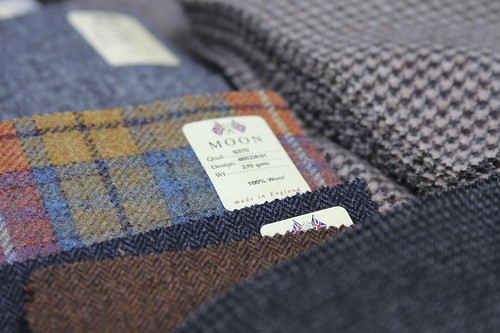
A selection of heritage fabrics on display.
As I walked through and looked on at each process of construction, the balance between old but proven techniques and machinery from various eras since the industrial revolution, really left a lasting impression on me. Quality begins on the sheep farms, the water used in the mill and Moons' honed processes from dye house to finishing. Each inch of fabric is inspected at the three main stages of the manufacturing process, when it comes off the loom, after finishing and again before it leaves the factory. With Moon you can be sure that you get nothing less than quality wool. I'll leave you a few close up shots of the finished lambswool fabrics used in the collaboration...
Moon is a company that continues to learn and strive for the highest quality. It was a real pleasure to watch them work and after spending a few hours there, it is obvious why Joe Casely-Hayford and John Lewis chose to work with them once again for this project. Next year Moon celebrates its one hundred and seventy fifth birthday, here's hoping to many more successful years of great British fabric production.
6 comments:
Great post! I'm also very keen in knowing how thing and specially shoes and fabrics are made.
Maybe you'll like a little post that I did about my visit to the Teviz Flannel Factory here in the North of Portugal.
http://www.ramalhoni.com/2011/10/ramalhoni-factory-visit-teviz.html
Cheers..
Miguel
this may well have been one of my fav SS posts ever. you captured the process so well, there's loads of hidden stuff i don't understand but i will never look at wool in the same light now. it's just incredible, feels quite special that it's still happening here too.
amazing.
Yes yes yes, this what we want to see! More factories, more making, more warp and more weft!
what a wonderful feature! so glad i discovered this blog, having lots of fun exploring it :)
Very nice blog...thank you for sharing..:)
Posts like this make me so giddy I have to lie down in a dark room with some incense and imagine Morgan Freeman reading to me.
Post a Comment