Exactly one week ago I shared the news that Joe Casely-Hayford for John Lewis would be returning for the new season. The sophomore collection of this intriguing collaboration once again celebrates true craftsmanship and home grown British manufacturing. With collaborations with remote mills in Yorkshire, tartan experts in Selkirk and respected bag maker Chapman to name but a few, the collection once again brings seemingly specialist products to a wider audience without losing any of the integrity that make their products special. The Cheaney brogues typify why this capsule collection is so exciting: the collaboration of great British design talent with heritage brands coming together for the high street. During my excited ramblings I mentioned the fact that I was invited to watch the Cheaney craftsmen at work at their Desborough factory. I eagerly followed and snapped away at each well honed and practiced process from start to finish in the factory that has been their home for well over two hundred years.
Before I offer an abundance of 'factory porn' and talk you through the processes of what makes Cheaney footwear special I have to acquaint you with the brand and give you a little background. The name might not feel that familiar on first reading but I'm quite sure that you've seen or indeed worn their work without even knowing it. In addition to making fine, bench made shoes under their own label, the factory sees them create footwear for the likes of Gieves & Hawkes, Paul Smith, Jeffrey West and more recently Lodger. As I strolled through the space and watched the one hundred plus workforce in action it became apparent that Cheaney are a classic English shoe brand undergoing something of a quiet and assured metamorphosis under the ownership of William and Jonathon Church. Founded in 1886 by two brothers, Joseph and Arthur Cheaney, Cheaney quickly became one of the premier shoemakers of England. It is their ability to blend the past with the future, using the finest materials available, which has enabled them to become and remain one of the premier producers of Goodyear welted shoes in the world today. On a point where some of their competitors have wandered, both William and Jonathan Church are fully committed to producing footwear entirely made in England. They believe that moving offshore would lose the essence of the brand. The craftsmanship and well honed skills are essential to the product and it was a pleasure to be able to watch it all unfold in a space that has seen the same processes come together for over two centuries. It is little wonder why Casely-Hayford partnered with them.
Cheaney represent the height of English Bench Made shoe making. It takes eight weeks to make a pair of Cheaney shoes, it involves around one hundred and sixty hand operations, from cutting the leather through to finishing, combining the best of contemporary design with superb quality. Given how much of a factory pervert I am, you can only imagine how many photographs I took as William Church guided me through and in to the nooks and crannies of this well oiled assembly line of true craftsmanship. I have managed to hone them down and will now use them to guide you through the main shoe making processes.
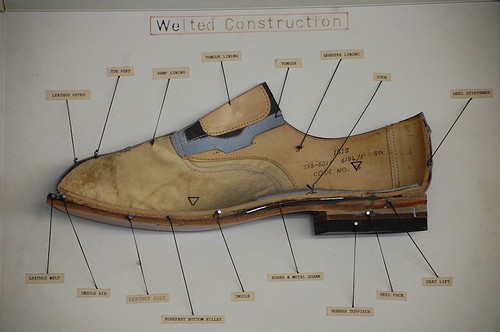
What makes a Goodyear wellted brogue?
The first construction stage is clicking and this is the process where the leather is cut. The term clicking refers to the sound made by the knife. Depending on the shoe, this stage can be performed by a press knife – a pneumatic machine that effectively punches through the leather like a cookie cutter or by hand and I watched both practices performed during my stay. It was amazing to watch how the craftsmen made use of the hide. During this stage it was different aspects of the hide and the fact that the skill of the craftsmen ensures that the best of the leather is used for the uppers (as a rule, the further back you go on the animal, the better the quality of skin) and that there is minimal wastage.
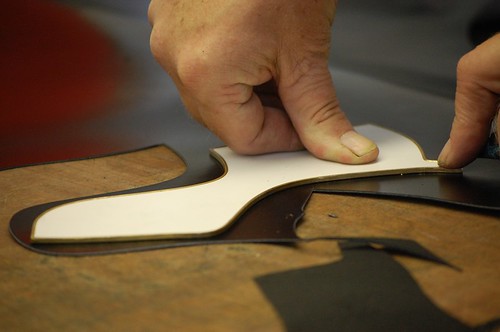
I was surprised at how much of this was still performed by hand.
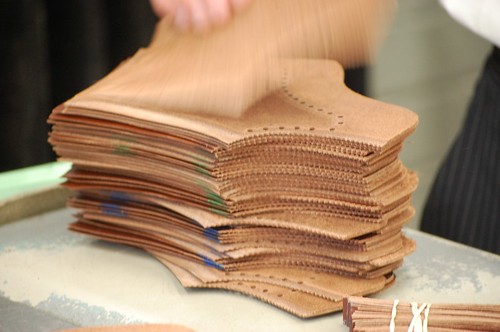
I took a peculiar amount of delight in marveling at this table of components
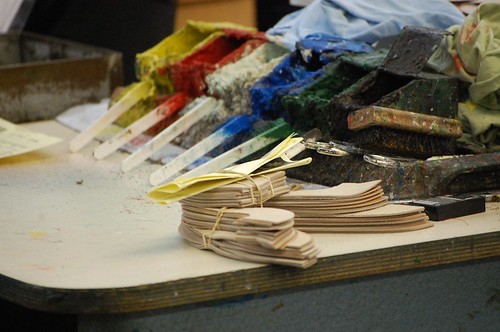
Clicked leather, ready for the next stage...
The next stage is closing. The is where the various parts of the upper are sewn together. With a bespoke shoe it would be done by hand, but every other type of shoe is closed by machine. I was amazed at how precisely yet quickly the machinists turned the clicked leather segments in to recognisable shoe forms.
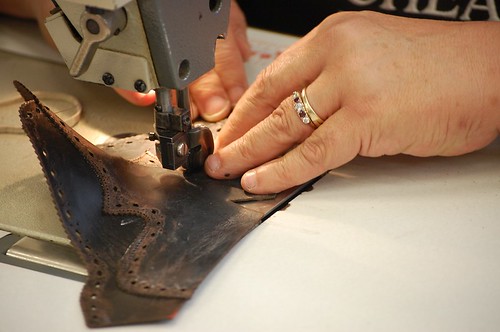
The upper begins to take shape.
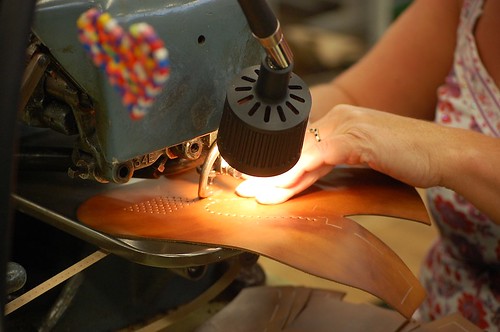
The embellishment of the upper.
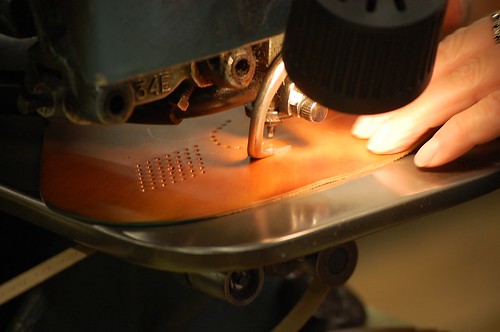
Given the intricacy of the pattern it was mind blowing to see how fast the ladies transformed the uppers.
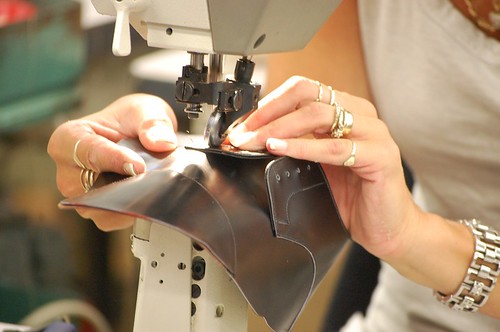
Another closing scene that is only just the beginning for this shoe.
The next stage is lasting. As I entered this intimidatingly large and machine heavy part of the factory I was instantly taken by the dominance of one gender, males. The prevalence of women in the 'closing' area had gone seemingly unnoticed but the moment I stepped in to this space, the lack of women was obvious. I'm just not used to being in such gender defined environments. As I manoeuvred my around the testosterone I was able to watch what makes Great British shoemaking so great.
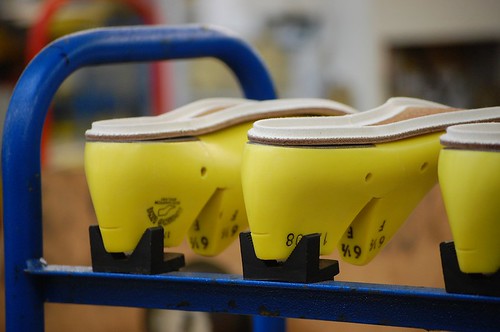
The lasts.
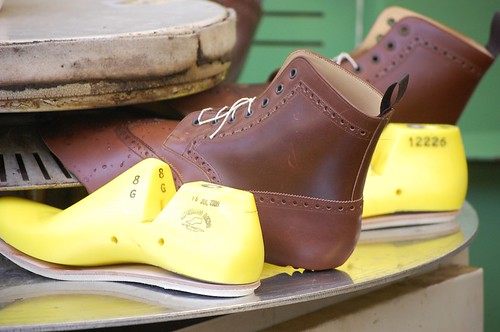
Throughout the shoe making process the leather loses moisture so here the uppers are placed in a steam machine to soften the leather.
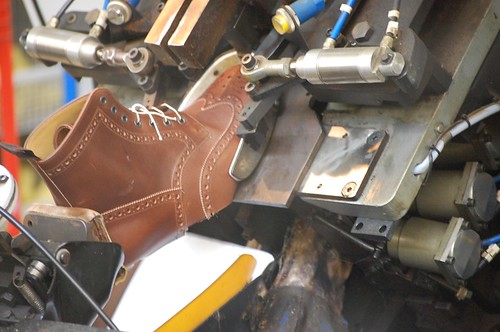
The uppers are then pressed and pinched on to the last...
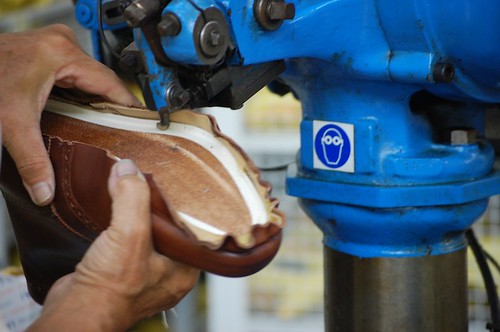
The shoe is readied for the welted sole with the help of a few staples...
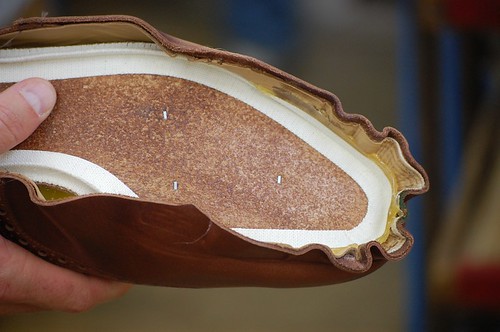
A closer look at the early stages of the lasting process.
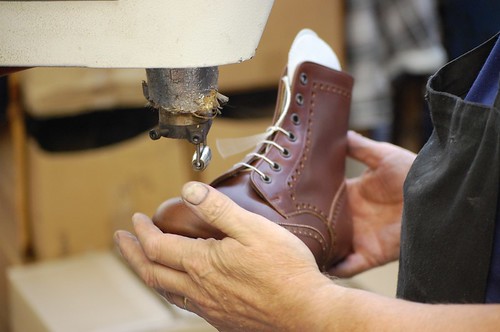
Any wrinkles are smoothed out before the iconic lasting stage...
Goodyear Welting is, after two hundred years of shoemaking in Northampton, still considered the finest method of shoe construction. Once the upper leather has been ‘closed’ it is placed onto the wooden last and the insole is attached. A strip of leather called the ‘welt’ is then stitched through the upper leather to the underside of the leather insole. The outer sole is then stitched to the welt. This ‘Goodyear welting’ is time consuming and requires highly skilled craftsmen. However it means the sole can be replaced time and again without damaging the upper leather. As the leather components are stitched rather than glued together all the natural properties of the leather are retained, giving superior thermal insulation, durability and shape retention, as well as the best possible breathing conditions for feet. The more a Goodyear Welted shoe is worn, the more comfortable it becomes as the leather components gradually mould to the shape of the foot.
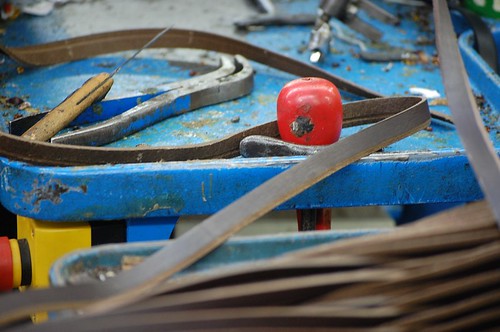
A closer look at the highly important welting.
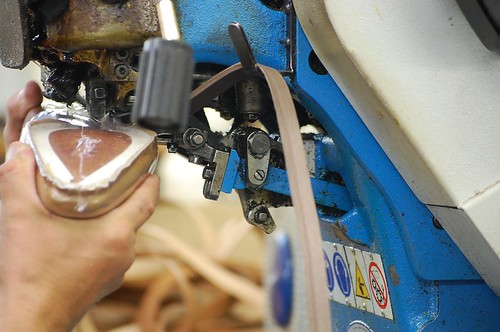
The welt is fed and stitched using this ingenious machine. I watched this process over and over again.
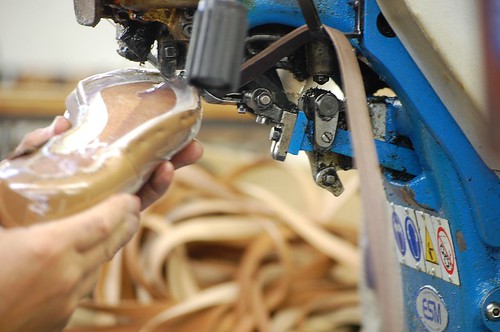
This process is so important to English shoe making
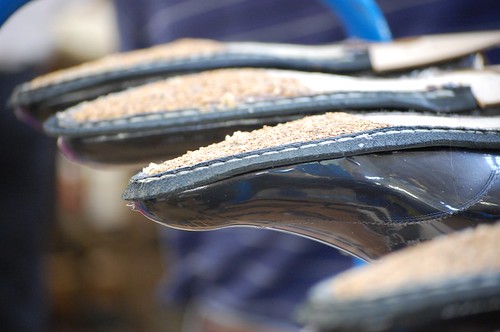
The under sole is then prepared for the outer shell.
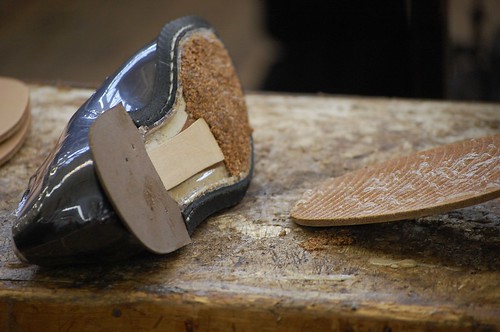
A strip of wood is inserted to ensure a better structure before the outer sole is glued in to place.
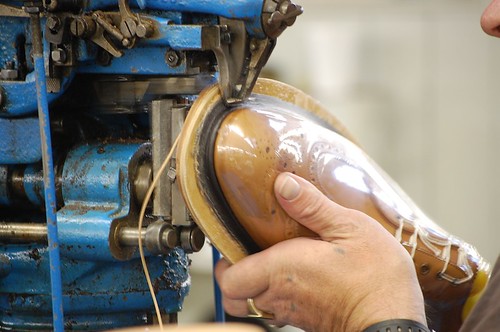
The excess from the outer sole is removed
The next stages sees the welt sewed to the upper, and both to the sole. I was told that doing this by hand takes a great deal of time and this is an area where industrial advancements have really helped. Each stitch has to be locked, using two threads that effectively create a knot at every stage. Doing it by machine takes a matter of minutes, so almost all bench made shoes do it this way. It is no less impressive though.
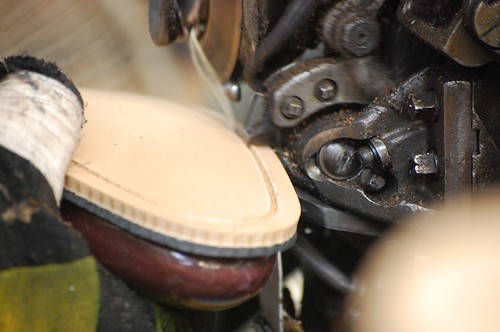
The machine in action
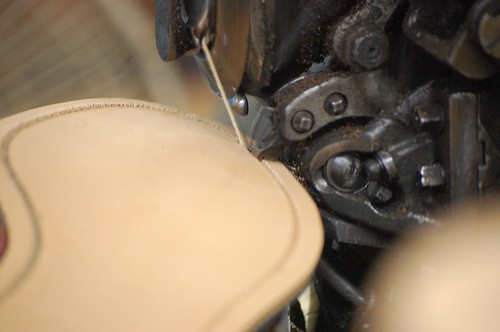
A closer look at how the stitching is locked
We then move on to the final two stages, the bevelling of the waist and polishing of the the upper. These processes should not be underestimated because they combine to provide the distinguishable aesthetic of English made shoes very special indeed. Bevelling is a particular treatment of the waist of the shoe, specifically that part of the sole at the waist lying between the flared-out ball-of-the-foot area and the heel. The treatment is one in which the sole at that point is shaped into a quite convex form, with the bottom of the curve right in the middle (from side to side), and the sole curving up at the edges.
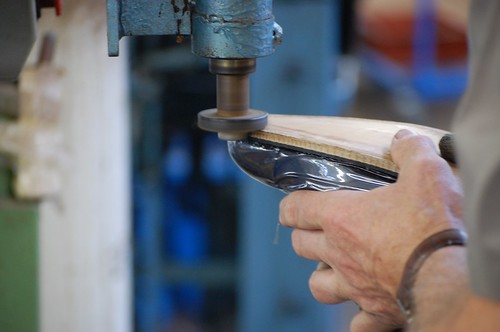
The sole and heel are sanded and smoothed using various machines.
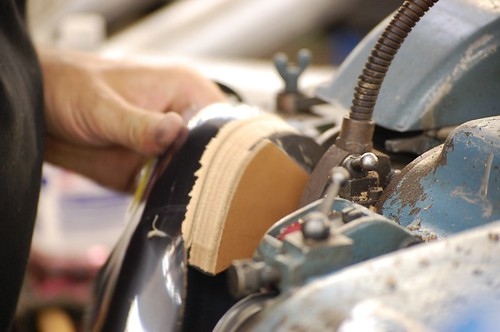
The heel takes shape.
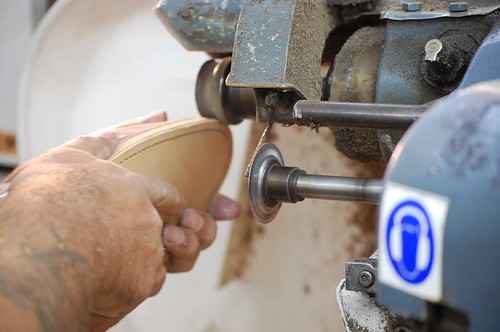
The surface is smoothed and rounded
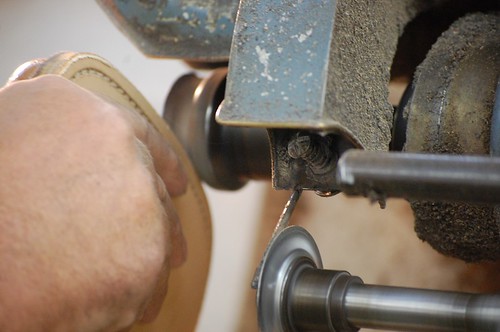
The attention to detail and reliance on the craftsman's eye are key at this point.
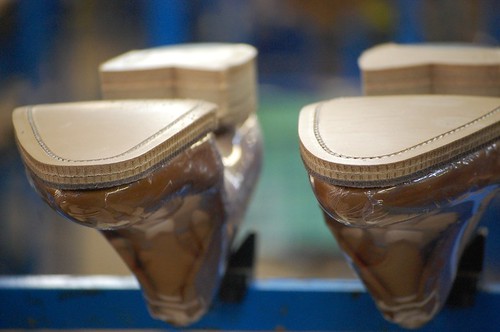
A more recognisable form. Simply stunning.
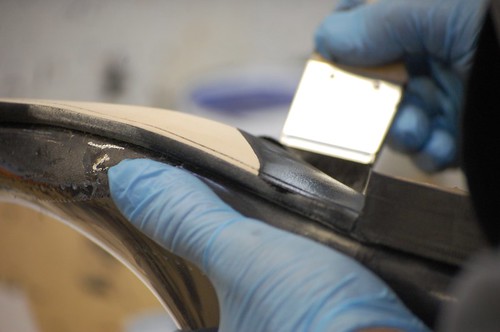
Applying the finishing touches to the sole.
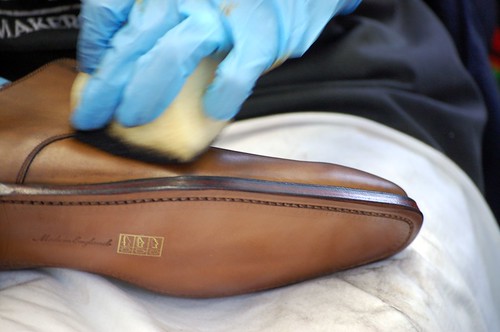
On to the burnishing of the upper. I've never seen polish applied so quickly and enthusiastically.
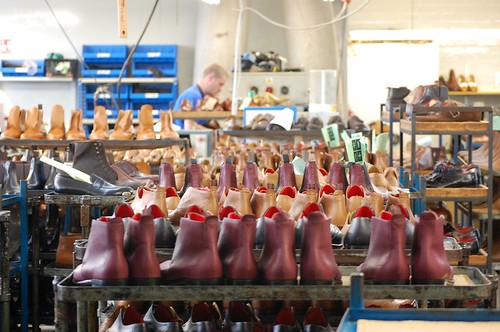
The final product ready for packing.
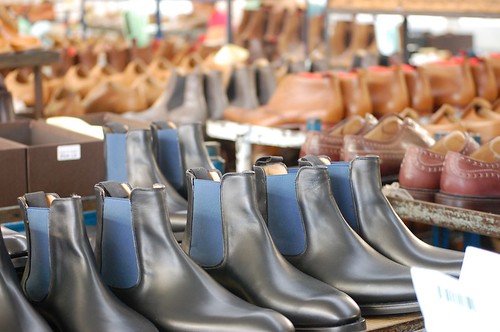
Notice the variety of designs.
During my time at the factory I was able to see firsthand snapshots of the creation process for the latest Joe Casely-Hayford for John Lewis, Cheaney brogue. The Mentor shoe is a new take on the classic Oxford. It showcases sophisticated design elements including an integral punched toe cap and a chamfered Goodyear Welted sole to make a shoe both wonderfully stylish yet practical. I was fortunate enough to view the finishing touches being applied to one of the final dozen due to be dispatched to John Lewis, ready for sale later this month...
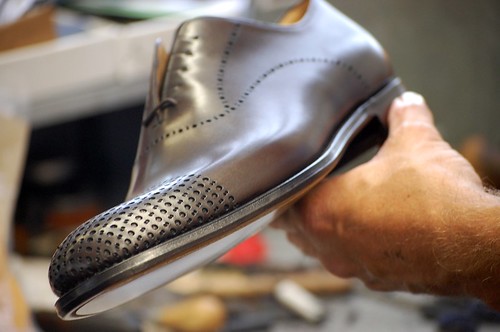
A final inspection.
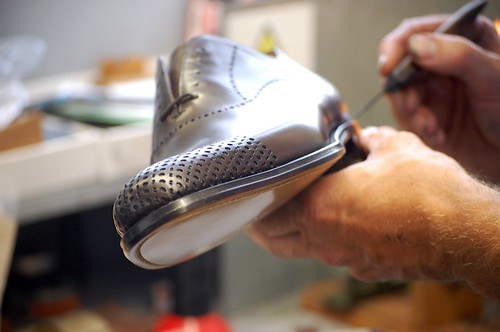
A quick finish to ensure perfection in each and every shoe.
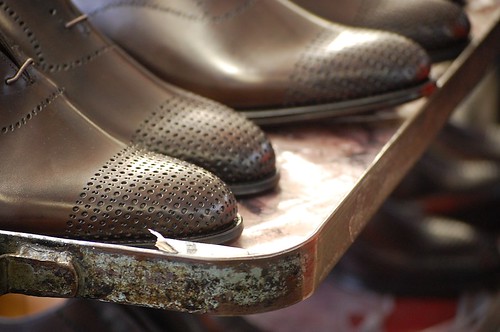
The Mentor shoe will be available to purchase very soon.
Using only the best available materials, including calf upper leather and oak bark tanned soles, Cheaney’s craftsmen apply their skills to produce handmade and benchmade shoes which maintain a standard seldom equalled in the world of Goodyear welted footwear. As I walked through and looked on at each process of construction, the balance between old but proven techniques and machinery from various eras since the industrial revolution, really left a lasting impression on me. This is a company that continues to learn and strive for the highest quality in an environment that has changed very little in well over two hundred years. It was a real pleasure to watch them work and after spending a few hours there, it is obvious why Joe Casely-Hayford chose to work with them once again for this project.
22 comments:
What a wonderful post, I never thought I'd find the shoe-making process so fascinating. And the thought of all this happening in a factory in England makes me very, very happy. Thank you!
Anna
Great post Steve, possibly your best yet. Facinating to read and great to finally see this process revealed in all it's detail.
A great read and beautiful images.
What a wonderful post, I never thought I'd find the shoe-making process so fascinating. And the thought of all this happening in a factory in England makes me very, very happy. Thank you!
I've been reading your blog for a long time now but this is the first time I've left a comment; this post is just so good that I had to say something!
I recently received my first pair of Lodgers so I really enjoyed these photos. I've also never been all that clear on Goodyear construction until reading this. Very informative!
John: Thank you, that means a lot.
Ernest: Thanks!
Anna: Ever since I visited John Smedley's factory Lea Mills I've been obsessed with factories. Shoe making is particularly interesting though, so much fun being able to watch a hide being transformed right in front of you.
Tom: Thanks, I really appreciate that. I know exactly what you mean, most people know the terms but few could really explain the process, I'm pleased that this post can help. Ooh and which Lodger's did you get?
best. post. ever.
are the church brothers that own cheaney's related in any to the classic english shoe brand church's (which is currently owned by prada)?
Donna: Ha, thanks! Yes, William Church is the great-great grandson of one of the three brothers who founded Church & Co in 1873, while Jonathan is his third cousin. The Church family still have extremely strong links with English shoe making.
Spectacular post, very inspiring. It's so rare to see such quality, let alone the process. Very interesting. Thank you very much!
Steve, I got the January SOMs - the canvas spectators. Apparently there were some problems in their construction (I don't know the specifics) which turned a three month wait into nearly six! Not that I'm complaining though. They were absolutely worth the wait, and everyone who I've spoken to at Lodger has been an absolute pleasure to deal with. Hopefully I can find some time next week to go and see their new range of shoes.
amazing post, i would love so much to visit a factory creating such fine pieces. i was watching a programme a couple of weeks ago about a bicycle factory in north england and this reminds me of it.
maybe one day i will be so lucky to witness the craftmanship
Nick: Thanks so much. The reaction to the post has been amazing. I'll hopefully be doing a lot more of these.
Tom: There are a few items in this world that are worth waiting for, quality shoes are certainly among them. I know the folks at Lodger well, Nathan and his team are great fun and their passion for shoes is infectious.
Mat: Thank you! I watched and enjoyed the bicycle shoe as well. This was such an enlightening experience. I had preconceptions of the factory being staffed only by ageing craftsman but the mix of ages is quite extraordinary. I meant to mention in the post that 90% of the people who work there live in a two mile radius. There is something very special about that stat.
My favouritest post in forever! Drool may have actually escaped the corner of my mouth.
Scrolling through those images was like one of those 'How do they make it' 5 mins documentaries on Ch4. But even better. :D
Jordan.
Steve,
Your eye and photography skills are incredible! You really do have an eye for detail and I definitely think you should continue these features you're doing on the art of craftsmanship. SHEER GENIUS!!!!
BTW, please do email me first when those Mentors go on sale. Do they come in other colors? ;)
Syed: Ha, what a lovely image!
Jordan: I love those so that's a huge compliment, thank you!
TommyTon: It is mighty odd waking up to a comment from you complimenting me on my photographic eye! Thanks though. Factory porn brings out the best in me and I'd love to do work on a lot more of these.
Of course I'll keep you updated on the Mentors, they'll be going on sale very, very soon. As for colours, they come in black as well as a espresso.
Great pictures, they really tell a story too. Chalk full of information, I had no idea there was so much involved. Thanks!
snappy x
www.snappylifestyle.blogspot.com
Bravo Steve.
Things like this remind me of more interesting things other than going through catwalk images and oggling at merchandise through online retailers.
What is often unseen has that much of an allure for someone like me who inevitably gets tired of fashion.
Great post, Steve!
wow, great post! i love seeing how things are made, i really admire how these people work.
This is my third visit to this post. Wow, stunning and informative. More of this please!
It's nice to see an old British company still doing well. Also interesting to see the manufacturing process
Post a Comment